Explore the Benefits of Alloy Nickel and Iron in Modern Tech
Updated: 09 Nov 2024
261
Introduction
Alloy nickel and iron are two powerful materials that play a vital role in industries and technologies around the world. These metals, when combined in various ratios, form alloys known for their exceptional strength, durability, and resistance to corrosion. Whether it’s the aerospace industry, manufacturing, or energy production, these alloys are crucial for creating components that can withstand extreme conditions, such as high temperatures and harsh environments.
Nickel adds superior corrosion resistance and heat tolerance to iron, making the combination perfect for applications in everything from engines to energy turbines and even in the construction of spacecraft. The versatility of iron-nickel alloys has made them essential in fields like electronics, automotive engineering, and even magnetic shielding materials. In this article, we will explore the unique properties of alloy nickel and iron, their applications, and why they are so highly valued across various industries.
What Is Alloy Nickel and Iron?
Alloy nickel and iron is a special type of metal that is made by combining two different metals nickel and iron. When mixed together, these metals form a new material that has some very useful qualities. For example, alloys made of nickel and iron are strong, resist rust, and can handle very hot temperatures without getting damaged. This makes them perfect for things like making engines, tools, and even parts of airplanes or rockets.

Alloy Nickel and Iron that we see in many everyday things, like nails and bicycles. But when we mix it with nickel, it becomes even more powerful and can be used in more important jobs. Nickel helps the iron to be better at resisting rust, especially when it is exposed to water or air. This is why you’ll find iron-nickel alloys being used in many important places, like in machines that work in the ocean, or in places where things get really hot.
You May Also Visit It!
Spray Arc Welding – Step by Step Guide – Need Metals
Pre Coat Metal | Define Complete Guide- Need Metals
Mcelroy Metals – Types, Uses And Properties – Need Metals
Will Magnets Stick to Stainless Steel Refrigerator – Complete Guide
Why Are Alloy Nickel and Iron Important?
Alloy Nickel and Iron are essential due to their ability to combine the strengths of both metals, resulting in a material that is not only strong and durable but also highly versatile. These alloys play a crucial role across various industries, particularly where performance under extreme conditions is vital.
1. Outstanding Strength and Durability
- Iron-nickel alloys are renowned for their superior strength. By merging iron and nickel, these alloys provide significantly better resistance to wear and tear than either metal alone. This durability makes them ideal for creating long-lasting components in machinery, vehicles, and construction equipment.
2. Corrosion Resistance
- The addition of nickel enhances the alloy’s resistance to corrosion, which is especially valuable in harsh environments such as saltwater or chemical exposure. This makes them perfect for applications like marine equipment and oil drilling tools, where untreated materials would quickly degrade without nickel’s protective properties.
3. High Heat Resistance
- Alloy nickel and iron excel in high-temperature environments without compromising their strength. This heat tolerance is critical for industries such as aerospace, where components need to endure extreme heat, such as those used in jet engines, turbines, and rocket nozzles.
4. Applications in Advanced Technology
- Iron-nickel alloys are integral to high-tech electronics, offering unique magnetic properties. They are used in applications such as magnetic shielding and precision instruments, where resistance to interference from magnetic fields is essential.
5. Versatility Across Industries
- Thanks to their combination of strength, heat resistance, and corrosion resistance, these alloys are valuable in numerous industries, including automotive, energy production, and medical technology. Maraging steel, a specific iron-nickel alloy, is even used in premium sports equipment like high-end golf clubs, offering an excellent balance of strength and flexibility.
The significance of alloy nickel and iron lies in their remarkable strength, durability, corrosion resistance, heat tolerance, and versatility. These qualities make them indispensable in producing everything from spacecraft to everyday tools, ensuring performance and longevity in demanding conditions.
Properties of Iron-Nickel Alloys
Alloy Nickel and Iron possess exceptional qualities that make them highly valuable across various industries. Here are the key properties that set these alloys apart:
1. Strength and Durability
Iron-nickel alloys are incredibly strong and resistant to breaking under stress. The combination of iron and nickel enhances their toughness, making them ideal for manufacturing long-lasting parts in machines, engines, and other high-demand applications.
2. Corrosion Resistance
One of the standout features of iron-nickel alloys is their enhanced resistance to rust and corrosion compared to pure iron. Nickel acts as a protective layer, preventing damage from exposure to moisture or air. This makes these alloys perfect for use in marine equipment, tools, and other applications in water-rich environments.
3. Heat Resistance
Iron-nickel alloys can withstand extremely high temperatures without losing their structural integrity. This property is particularly valuable in industries like aerospace, where components such as jet engines, turbines, and spacecraft parts must endure intense heat while maintaining strength.
4. Magnetic Properties
Certain iron-nickel alloys possess unique magnetic properties, enabling them to attract magnets or block magnetic fields. These properties are crucial for applications like magnetic shielding in electronics and tools that need to function around magnetic forces.
5. Low Expansion
Some iron-nickel alloys, such as Invar, have a minimal expansion rate when exposed to heat. This makes them ideal for use in precision instruments, clocks, and spacecraft, where even the smallest changes in size can affect performance.
Alloy Nickel and Iron offer a combination of strength, corrosion resistance, heat tolerance, magnetic capabilities, and low thermal expansion, making them indispensable in applications ranging from aerospace to high-tech equipment.
Types of Iron-Nickel Alloys
Iron-nickel alloys come in various types, each designed for specific applications by adjusting the proportion of nickel mixed with iron. Here are some of the most common types:
1. Pure Iron-Nickel Alloys
These alloys are made with a basic mixture of iron and nickel. The nickel content can vary, but these alloys are generally crafted to offer enhanced strength and corrosion resistance compared to pure iron. They are widely used in general manufacturing and industrial applications, such as producing tools and components that require durability and longevity.
2. Invar (Low Expansion Alloys)
Invar is a unique iron-nickel alloy known for its minimal expansion when heated. This property is especially useful in situations where precise size stability is crucial, such as in precision instruments, clocks, and aerospace applications. Invar’s ability to maintain its size under extreme temperature fluctuations makes it ideal for spacecraft and satellite components.
3. Hastelloy
Hastelloy is a highly corrosion-resistant iron-nickel alloy that includes additional metals like molybdenum. It is commonly used in harsh environments, such as chemical processing plants and aircraft engines, due to its ability to withstand high temperatures and aggressive chemicals. This makes it perfect for engine parts and equipment exposed to extreme conditions.
4. Maraging Steel
Maraging steel is a high-strength iron-nickel alloy that hardens without compromising its toughness. It is renowned for its strength and flexibility, making it ideal for use in high-performance sports equipment like golf clubs, as well as in aerospace and military applications. This alloy is designed to endure impact without cracking, combining durability with resilience.
5. Nichrome (Nickel-Chromium Alloys)
Nichrome, primarily composed of nickel and chromium, is a type of iron-nickel alloy used in heating elements. Its excellent resistance to heat and oxidation makes it perfect for applications like toasters, electric stoves, and industrial furnaces, where it must withstand high temperatures without degrading.
Alloy Nickel and Iron come in various forms tailored to meet specific needs, from precision tools to industrial heating elements. These alloys enhance strength, durability, and performance, making them invaluable in a wide range of demanding applications.
Applications of Iron-Nickel Alloys
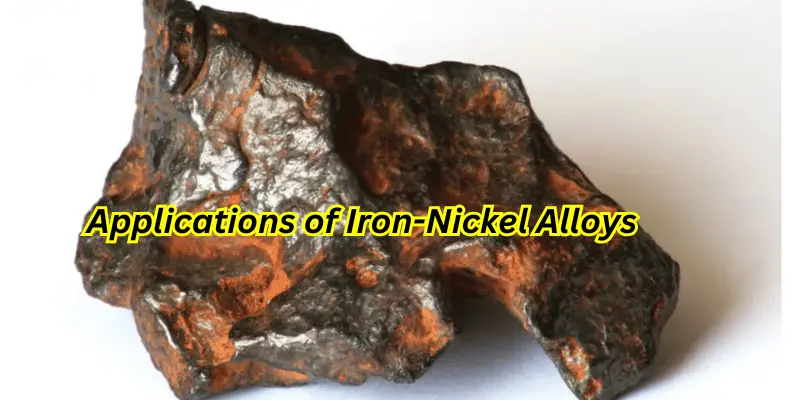
Iron-nickel alloys are used across a wide range of industries due to their unique properties, such as strength, corrosion resistance, and heat tolerance. Here are some key areas where these alloys play a crucial role:
1. Aerospace and Space Exploration
Iron-nickel alloys are commonly found in aircraft, rockets, and spacecraft due to their ability to withstand extreme temperatures and harsh conditions. For instance, Invar, known for its minimal thermal expansion, is used in satellites and space probes to ensure their components maintain their size and shape, even in fluctuating temperatures in space.
2. Marine Equipment
Thanks to their excellent corrosion resistance, iron-nickel alloys are widely used in marine applications, including ship parts and offshore drilling tools. These alloys are highly resistant to the corrosive effects of saltwater, making them essential for parts exposed to marine environments.
3. Automobile and Engine Parts
The strength and heat resistance of iron-nickel alloys make them ideal for automotive and industrial engine components, such as car engines and turbines. These alloys help engine parts perform better and last longer under the high heat and pressure typical in these applications.
4. Medical Equipment
Iron-nickel alloys, particularly stainless steel (which combines iron, nickel, and other metals), are commonly used in medical devices. Their durability, biocompatibility, and resistance to corrosion make them ideal for surgical tools, implants, and other medical equipment that must endure in sterile environments and resist infection.
5. Magnetic Applications
Certain iron-nickel alloys, like permalloy, are key components in magnetic devices. These alloys are used in making transformers, motors, and magnetic shielding, as they effectively resist interference from magnetic fields and are critical in the performance of electronic devices.
6. Electronics and Electrical Equipment
Iron-nickel alloys are used in various electrical and electronic components that require resistance to heat and corrosion. For example, nichrome, an alloy of nickel and chromium, is commonly found in heating elements such as those used in toasters, hairdryers, and industrial furnaces due to its ability to handle high temperatures safely.
Iron-nickel alloys are essential in many fields, from aerospace and marine equipment to medical devices and electronics. Their versatility and durability make them indispensable in both everyday technology and specialized industries.
You May Also Visit It!
Forging Process | Metal Becomes Tools and Parts – Easy Explanation
History of Nickel | From Ancient Coins to Modern Technology
Metal Does a Magnet Not Stick To | Uses and Types
Physical Properties Are Shared by Most Metals
Advantages and Disadvantages of Alloy Nickel and Iron
Iron-nickel alloys are known for their exceptional properties, but like any material, they come with both benefits and limitations.
Advantages of Alloy Nickel and Iron
Advantages |
---|
|
Disadvantages of Alloy Nickel and Iron
Disadvantages |
---|
|
Iron-nickel alloys offer impressive qualities such as strength, corrosion resistance, and heat tolerance, making them essential in numerous industries. However, their higher cost, brittleness, and processing challenges need to be considered when selecting the appropriate material for specific applications.
Common FAQs about Alloy Nickel and Iron
1. What is an iron-nickel alloy?
An iron-nickel alloy is a metal mixture composed primarily of iron and nickel in varying proportions. These alloys are known for their strength, resistance to corrosion, and ability to withstand high temperatures, making them essential in industries such as aerospace, automotive, and medical devices.
2. What are some common uses of iron-nickel alloys?
Iron-nickel alloys are used in a variety of applications, including aircraft, spacecraft, engines, medical devices, marine equipment, and heating elements like toasters. Their ability to resist heat, corrosion, and extreme conditions makes them highly suitable for these uses.
3. What are the main advantages of iron-nickel alloys?
The key benefits of iron-nickel alloys include:
- Strength: They are incredibly strong and durable.
- Corrosion Resistance: They resist rust, even in harsh environments.
- Heat Resistance: They can withstand extremely high temperatures.
- Magnetic Properties: Certain types are ideal for use in electronic devices and transformers.
4. Are there any disadvantages to using iron-nickel alloys?
Yes, some of the drawbacks include:
- Cost: They can be more expensive than other alloys.
- Brittleness: Certain types may crack or break under stress.
- Weight: They can be heavier compared to other materials.
- Difficult to Process: Some alloys require specialized tools and skills for processing.
5. What is the difference between Invar and other iron-nickel alloys?
Invar is a specific iron-nickel alloy known for its low thermal expansion. It remains almost unchanged in size when heated, making it ideal for precision instruments like clocks, measuring devices, and spacecraft components.
6. Can iron-nickel alloys be recycled?
Yes, iron-nickel alloys can be recycled, though the process may be more complex compared to recycling pure metals. Proper separation is crucial to ensure the alloys maintain their quality and can be reused effectively.
7. Is iron-nickel alloy the same as stainless steel?
While both iron-nickel alloys and stainless steel share some similarities, stainless steel typically contains iron, nickel, and chromium, while iron-nickel alloys may or may not include chromium. Both materials are prized for their strength, durability, and resistance to rust.
8. How does the amount of nickel affect the properties of the alloy?
The nickel content significantly influences the properties of the alloy:
- A higher nickel content enhances the alloy’s strength, heat resistance, and corrosion resistance.
- It can also impact the alloy’s magnetic properties and flexibility.
These FAQs highlight the versatility of iron-nickel alloys, showcasing their valuable applications across multiple industries, while also noting the importance of considering factors like cost and processing challenges when choosing these materials for specific tasks.
Bonus Points
- Low Expansion: Certain iron-nickel alloys, such as Invar, are renowned for their extremely low expansion when heated. This property makes them perfect for precision instruments and devices that require highly accurate measurements, like scientific tools and components for spacecraft.
- Presence in Meteorites: Iron-nickel alloys aren’t just found on Earth—they are also naturally occurring in meteorites and are thought to be present in the cores of planets, including our own. This natural occurrence makes them crucial for understanding the formation of the solar system.
- Magnetic Applications: Some iron-nickel alloys possess unique magnetic properties that make them ideal for use in electrical devices such as transformers and motors. For instance, mu-metal, a specific iron-nickel alloy, is frequently used in magnetic shielding due to its high permeability.
- Customization for Specific Needs: The properties of iron-nickel alloys can be tailored by adjusting the ratio of iron to nickel. This flexibility allows manufacturers to create alloys suited to particular applications, whether they are needed for high-stress machinery or parts that need to resist corrosion.
- Environmental Impact: While iron-nickel alloys are highly durable and reduce the need for frequent replacements, they remain a non-renewable resource. Efforts are being made to enhance recycling methods, ensuring that these materials can be reused more sustainably.
Conclusion
Iron nickel alloys are special metal mixtures made of iron and nickel, valued for their strength, resistance to rust, and ability to handle high temperatures. They are used in many important areas like aerospace, automotive, and medical devices.
While these alloys offer great advantages, such as durability and heat resistance, they can also be expensive and may have some challenges, like brittleness or difficulty in processing. Overall, iron-nickel alloys are essential materials in modern technology, providing solutions where other materials might not perform as well.
You May Also Visit It!
Magnetic Materials | What Materials Are Attracted By Magnets – Benefits
Yield Strength of Metals: Types, Uses and Clear and Simple Overview
Heat Treating Steel | Key Temperatures for Hardening, Types and Uses
1075 or 1095 Steel | Find the Best Steel for Your Knife
Aluminium Metal, Types, Uses, Properties and Rust Aluminium
Please Write Your Comments