Plasma Cutter How Does It Work – Complete Guide
Updated: 27 Oct 2024
222
Plasma cutter how does it work have you ever seen a magic trick where something appears to be sliced effortlessly? That’s similar to what happens when a plasma cutter goes to work! This amazing tool is like a superhero for metal, using a special kind of hot gas called plasma to cut through materials like steel and aluminum. But how does it do that?
Plasma cutting starts with an electric arc that heats up the gas, turning it into plasma, which can reach temperatures hotter than the sun! This super-hot plasma creates a powerful jet that melts the metal and blows it away, leaving behind a clean and precise cut. It’s not just a tool for professionals; many DIY enthusiasts and artists use plasma cutters to bring their creative projects to life.
We’ll explore the fascinating world of plasma cutters, how they work, and why they are such an important tool in metalworking today.
Table of Contents
What is a Plasma Cutter and How Does It Work?
A plasma cutter is a special tool that helps people cut through metal quickly and easily. Imagine it like a superhero for metal pieces! It uses something called plasma, which is a super-hot gas, to slice through materials like steel and aluminum.
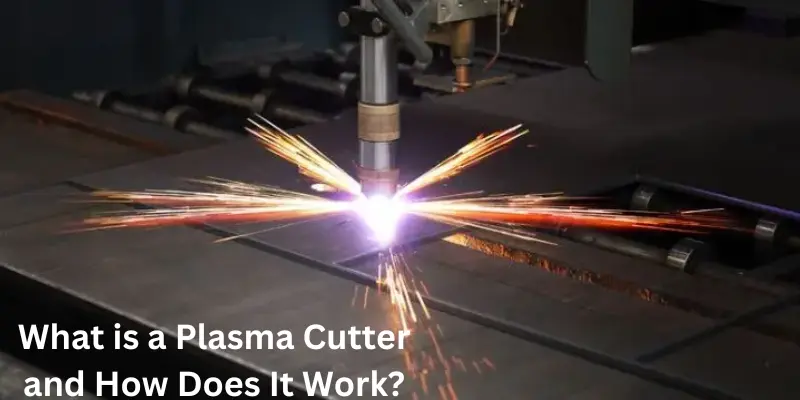
So, how does it work? First, the plasma cutter creates a spark of electricity that turns the air around it into plasma. This plasma can get really, really hot—hotter than the surface of the sun! When the plasma jet hits the metal, it melts it almost instantly. Then, the powerful blast of gas pushes the melted metal away, making a clean cut.
Plasma cutters are great for many jobs. They can help artists create amazing metal sculptures, mechanics fix cars, and builders make strong structures. With this tool, you can turn your big ideas into real creations!
You May Also Visit It!
Spray Arc Welding – Step by Step Guide – Need Metals
Pre Coat Metal | Define Complete Guide- Need Metals
Mcelroy Metals – Types, Uses And Properties – Need Metals
Will Magnets Stick to Stainless Steel Refrigerator – Complete Guide
Why is Plasma Cutter How Does It Work Important?
Plasma cutting is an essential technology in many industries, and understanding its importance can help you see how it impacts our daily lives. Here are some reasons why plasma cutters are valuable:
- Speed and Efficiency: Plasma cutters can slice through metal much faster than traditional cutting methods, making them ideal for projects that need to be completed quickly. This speed saves time and increases productivity in workshops and factories.
- Precision Cuts: They can create clean and precise cuts, which means less time is spent on finishing work. This precision is crucial for tasks that require accuracy, such as building vehicles or creating intricate designs.
- Versatility: Plasma cutters can cut various materials, including different types of metals. Whether it’s thin sheets or thick metal plates, this tool can handle a wide range of projects, making it a favorite among artists, builders, and manufacturers.
- Cost-Effectiveness: While plasma cutters can be an investment, they often reduce labor costs because they are quicker and easier to use. This efficiency means fewer people are needed to get the job done, which can save money in the long run.
- Widespread Use: From automotive repair shops to art studios, plasma cutters are used in various fields. Understanding how they work can open up many career possibilities in welding, fabrication, and design.
Plasma cutting is important because it offers speed, precision, versatility, cost savings, and a wide range of applications in different industries.
Plasma Cutter How Does It Work and Its Types?
Plasma cutters are amazing tools, but did you know there are different types? Each type works a bit differently, but they all use plasma to cut through metal. Let’s explore how they work and the different types you might come across!
How Plasma Cutters Work
At the heart of every plasma cutter is a simple process:
- Creating Plasma: The plasma cutter starts by generating an electric arc. This arc heats the air around it, turning it into plasma, which is a super-hot gas.
- Cutting Through Metal: The plasma jet shoots out, reaching temperatures that can melt metal almost instantly. When the jet hits the metal, it melts it, and the force of the plasma blows the melted metal away, creating a clean cut.
Types of Plasma Cutter How Does It Work
- Air Plasma Cutters
- These are the most common type. They use compressed air as the gas to create plasma.
- They are great for cutting thinner materials, making them perfect for hobbyists and smaller projects.
- Water Plasma Cutters
- These use water along with the plasma to cool the cutting area.
- This type is helpful because it reduces the amount of smoke and debris created while cutting, making it cleaner and safer to use.
- Dual Gas Plasma Cutters
- These machines can switch between two gases, usually air and an inert gas like nitrogen.
- They offer more flexibility, allowing you to choose the best gas for different types of materials.
- High-Definition Plasma Cutters
- These are more advanced and can cut through thicker materials with even greater precision.
- They are used in industrial settings where high-quality cuts are essential.
- Handheld Plasma Cutters
- These are portable and easy to use, making them popular for DIY projects and repair work.
- They allow you to move around and cut wherever you need, which is great for smaller tasks.
Each type of plasma cutter has its own advantages, making them suitable for different projects and materials.
Uses of Plasma Cutter How Does It Work
Plasma cutters are super useful tools that help people in many different fields. Here are some of the exciting ways they are used:
- Metal Fabrication
- Plasma cutters are often used in factories to create parts for machines, cars, and buildings. They help shape metal quickly and accurately, making it easier to put everything together.
- Art and Sculpture
- Many artists use plasma cutters to create stunning metal sculptures and artwork. The precision of the cuts allows them to make intricate designs that stand out in galleries and public spaces.
- Automotive Repair
- Mechanics use plasma cutters to fix cars and trucks. They can cut through thick metal quickly to remove damaged parts or to make new pieces that fit perfectly.
- Construction
- In construction, plasma cutters are used to cut steel beams and sheets. This helps builders create strong and safe structures, from bridges to skyscrapers.
- Aerospace
- The aerospace industry relies on plasma cutting to shape metal parts for airplanes and spacecraft. These parts need to be super precise, and plasma cutters help ensure that they fit together perfectly.
- DIY Projects
- For hobbyists and DIY enthusiasts, plasma cutters are great for home projects. Whether making custom furniture or outdoor decorations, these tools can turn creative ideas into reality.
- Shipbuilding
- Plasma cutters are also used in shipyards to cut large metal sheets and plates for building ships. This speeds up the construction process and helps create sturdy vessels.
Plasma cutters are amazing tools that make many jobs easier and faster, whether in factories, workshops, or art studios. Their ability to cut metal with precision means they are essential in lots of different industries!
You May Also Visit It!
Forging Process | Metal Becomes Tools and Parts – Easy Explanation
History of Nickel | From Ancient Coins to Modern Technology
Metal Does a Magnet Not Stick To | Uses and Types
Physical Properties Are Shared by Most Metals
Making Process of Plasma Cutter How Does It Work

The making process of plasma cutters involves several important steps that help create this amazing tool. Here’s a simple breakdown of how plasma cutters are made:
- Designing the Cutter
- Engineers start by designing the plasma cutter on computers. They create blueprints that show how the machine will look and work. This step is super important because it helps ensure everything fits together perfectly.
- Gathering Materials
- Once the design is ready, manufacturers gather all the necessary materials. Plasma cutters are made from strong metals and special components like electric wires, valves, and a power supply. These materials help the cutter produce the hot plasma needed for cutting.
- Assembling Parts
- The next step is assembling all the parts. Workers put together the main body of the plasma cutter, installing components like the torch (the part that creates the plasma jet) and the cooling system. This is like building a complex puzzle where each piece has to fit just right!
- Testing the Equipment
- After assembly, the plasma cutter goes through a series of tests to ensure it works properly. Technicians check to see if the plasma cutter creates the right temperature and pressure needed to cut through metal. They also make sure all the parts work together smoothly.
- Quality Control
- Quality control is a crucial step. Inspectors carefully examine each plasma cutter to make sure it meets safety and performance standards. They look for any flaws or defects that could affect how the machine works. Only the best cutters are sent out for sale!
- Packaging and Shipping
- Once everything is approved, the plasma cutters are cleaned, packaged, and prepared for shipping. They are carefully placed in boxes to keep them safe during transportation. Then, they are sent out to stores or customers around the world.
And that’s how plasma cutters are made! From design to testing, each step is important to create a reliable tool that helps people cut through metal with ease.
Properties of Plasma Cutter How Does It Work
Plasma cutters have some special properties that make them really effective at cutting through metal. Let’s explore these properties in a way that’s easy to understand!
- High Temperature
- Plasma cutters can reach extremely high temperatures—hot enough to melt metal! The plasma jet can be around 20,000 degrees Celsius (36,000 degrees Fahrenheit). This intense heat allows the cutter to slice through even thick metal quickly.
- Speed
- Plasma cutting is one of the fastest ways to cut metal. The quick action of the plasma jet means that projects can be completed much sooner than if you used other methods, like saws or torches. This speed is super helpful in busy factories and workshops.
- Precision
- Plasma cutters can make very accurate cuts. They can create sharp edges and detailed shapes without leaving rough spots. This precision is important, especially for jobs that need to fit perfectly together, like in car manufacturing or metal art.
- Versatility
- Plasma cutters can work with a variety of metals, including steel, aluminum, and copper. They can also handle different thicknesses of materials, making them useful for many different projects—from large industrial jobs to small DIY crafts.
- Portable Options
- Some plasma cutters are lightweight and designed to be portable, which means you can take them to different job sites. This flexibility is great for contractors and artists who need to work in various locations.
- Clean Cutting
- One of the best properties of plasma cutters is that they produce very little waste. The cutting process generates minimal slag (melted metal that can stick to the cut edges), resulting in cleaner cuts and less cleanup afterward.
- Safety Features
- Modern plasma cutters come with safety features like automatic shut-off systems and protective casings. These features help keep users safe while working with such powerful tools.
These properties make plasma cutters essential tools in many industries and for DIY projects. Their high temperature, speed, precision, and versatility allow them to tackle a wide range of metal cutting tasks effectively.
Conclusion
Plasma cutters are powerful tools that can cut through metal quickly and accurately. They are versatile and create very little waste, making them great for many projects. However, they can be expensive and require some skill to use safely.
It’s important to weigh the advantages and disadvantages before deciding if a plasma cutter is right for you. By understanding how they work and their properties, you can make an informed choice for your metalworking needs.
Bonus Point
- Environmentally Friendly: Plasma cutting generates less waste and fewer harmful fumes compared to traditional cutting methods, making it a greener choice for metalworking.
- Customization Options: Many plasma cutters come with adjustable settings for cutting speed and amperage, allowing users to customize the tool for different materials and thicknesses.
- Low Operating Costs: Although the initial investment can be high, plasma cutters often have lower operating costs due to their efficiency and speed, which can save money in the long run.
- Minimal Cleanup: The cutting process produces less slag and debris, reducing the time spent on post-cutting cleanup.
- Wide Range of Applications: Plasma cutters are used in various industries, including automotive, construction, and manufacturing, making them versatile tools for professionals and hobbyists alike.
- User-Friendly Technology: Many modern plasma cutters feature user-friendly interfaces and automatic settings, making it easier for beginners to get started with cutting.
You May Also Visit It!
Magnetic Materials | What Materials Are Attracted By Magnets – Benefits
Yield Strength of Metals: Types, Uses and Clear and Simple Overview
Heat Treating Steel | Key Temperatures for Hardening, Types and Uses
1075 or 1095 Steel | Find the Best Steel for Your Knife
Aluminium Metal, Types, Uses, Properties and Rust Aluminium
Please Write Your Comments