How to Master Sheet Metal Aluminum Gauge for Better Builds
Updated: 08 Nov 2024
500
Introduction
When working with aluminum for various projects, understanding the sheet metal aluminum gauge is essential for achieving the right balance of strength, weight, and cost. The gauge of aluminum refers to its thickness, and it plays a crucial role in determining how the material will perform under pressure, how much it will weigh, and how much it will cost. But heres the catch gauge numbers don’t follow the same rules across different types of metals. For instance, an 18-gauge aluminum sheet is thinner than an 18-gauge steel sheet.
Knowing how to read and choose the correct aluminum gauge can make a huge difference in the success of your project. Whether you’re working on construction, automotive, or even aerospace applications, the right gauge can ensure durability, cost-effectiveness, and ease of use. In this guide, we’ll explore the different aluminum gauges, how to select the ideal thickness for your needs, and provide helpful tips to ensure your next project goes smoothly. Understanding these basics will help you make informed decisions and get the best results from your aluminum sheet metal.
What Is Sheet Metal Aluminum Gauge?
Sheet metal aluminum gauge is simply a way to measure how thick or thin a piece of aluminum metal is. The term “gauge” refers to the number that tells you how thick the metal is: the higher the number, the thinner the metal, and the lower the number, the thicker it is. For example, a 10-gauge aluminum sheet is thicker than an 18-gauge aluminum sheet.
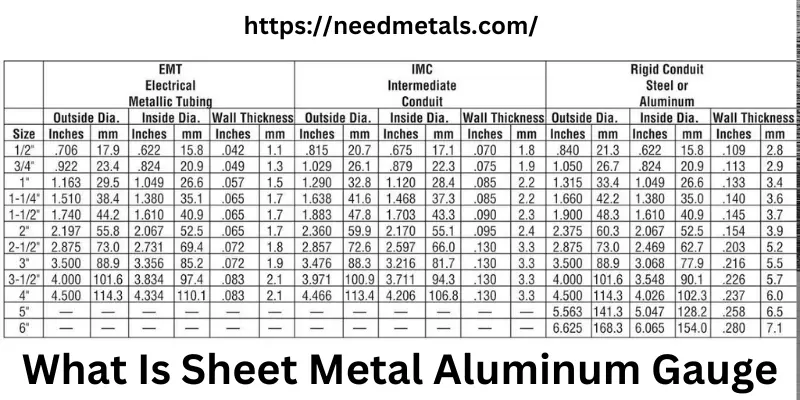
This measurement is important because the thickness of aluminum affects how strong, light, and flexible it is. For some jobs, like building cars or airplanes, you might need thicker aluminum to make sure it’s strong enough. For other projects, like making cans or foil, you might use thinner aluminum.
So, when you’re choosing aluminum for a project, it’s important to know what gauge you need to get the right thickness for the job.
You May Also Visit It!
Spray Arc Welding – Step by Step Guide – Need Metals
Pre Coat Metal | Define Complete Guide- Need Metals
Mcelroy Metals – Types, Uses And Properties – Need Metals
Will Magnets Stick to Stainless Steel Refrigerator – Complete Guide
Why Is Sheet Metal Aluminum Gauge Important?
The aluminum gauge for sheet metal is essential when selecting the right material for your project. The gauge number determines the thickness of the aluminum, which in turn affects several key factors such as strength, weight, cost, and workability.
1. Strength and Durability
- Thicker Gauges (lower numbers like 10 or 12): Offer greater strength, making them ideal for heavy-duty applications such as structural components in buildings or vehicles.
- Thinner Gauges (higher numbers like 18 or 20): Best suited for lighter, more flexible applications like household items, packaging, or aluminum foil.
2. Weight Considerations
The thickness of the aluminum directly impacts its weight. For example, thicker sheets weigh more, which may not be suitable for projects that require lightweight materials, such as in aerospace or automotive industries. Selecting the right gauge ensures an optimal balance between strength and weight for specific needs.
3. Cost Efficiency
Thinner gauges tend to be less expensive than thicker ones. By choosing the right thickness, you can control costs without sacrificing quality or performance.
4. Ease of Handling and Workability
Thinner aluminum is easier to cut, bend, and shape, making it ideal for projects that require precision and flexibility. In contrast, thicker gauges may need more effort and specialized equipment for shaping but offer superior performance in load-bearing situations.
5. Suitability for Specific Applications
Choosing the correct gauge ensures optimal performance in its intended environment:
- In construction, thicker aluminum is necessary to support heavy loads.
- In automotive and aerospace, thinner, lighter aluminum helps reduce weight while maintaining strength.
By carefully selecting the right aluminum gauge, you can ensure your project meets the required performance, cost, and durability specifications.
Types of Sheet Metal Aluminum Gauge Systems
When talking about Sheet Metal Aluminum Gauge, there are two main systems used to measure the thickness of the metal: the American Wire Gauge (AWG) and the Standard Wire Gauge (SWG). Both systems help us figure out how thick or thin the aluminum is, but they are a little different from each other. Let’s look at both:
1. American Wire Gauge (AWG)
- AWG is the system mostly used in the United States for measuring the thickness of metals like aluminum and copper.
- In this system, the higher the number, the thinner the metal. For example, a 10-gauge aluminum sheet is thicker than a 20-gauge sheet.
- AWG is mainly used for wires and sheet metal in industries like construction, electronics, and automotive.
2. Standard Wire Gauge (SWG)
- SWG is a system that was once used in the UK and some other countries. It also helps to measure the thickness of materials like aluminum.
- In the SWG system, the numbers also work in reverse: the higher the number, the thinner the material.
- It is often used in industries that deal with thicker metals and sometimes for crafts or jewelry making.
Key Difference:
- The main difference between AWG and SWG is the way they measure thickness. They use slightly different rules, so sometimes an aluminum sheet measured using AWG might not be the exact same thickness as one measured in SWG for the same number.
Its important to know which system is being used for your project, so you can be sure you’re choosing the right thickness of aluminum for the job.
Common Sheet Metal Aluminum Gauge and Their Applications
Different aluminum sheet gauges are used for different types of projects. The gauge number tells you how thick or thin the aluminum is, and each thickness is best for certain uses. Here’s a quick guide to some of the most common aluminum sheet gauges and where they are used:
1. 10-Gauge Aluminum
Thickness: 0.1345 inches (3.42 mm)
Applications:
- Used for heavy-duty tasks like building structural components (e.g., in construction or large machinery).
- Works well for making truck bodies, trailers, and other industrial products that need a strong, thick material.
Why Its Used: Its strong and durable, able to handle heavy loads without bending or breaking.
2. 12-Gauge Aluminum
Thickness: 0.1046 inches (2.66 mm)
Applications:
- Commonly used in automotive parts, doors, and panels.
- Great for protective covers and siding on buildings.
Why Its Used: It provides strength for outdoor and industrial uses but is still lightweight enough for easy handling.
3. 14-Gauge Aluminum
Thickness: 0.0747 inches (1.90 mm)
Applications:
- Often used for light-duty parts in vehicles and storage boxes.
- Suitable for HVAC (heating, ventilation, and air conditioning) ductwork.
Why Its Used: Its strong enough for these jobs while being flexible for shaping and cutting.
4. 16-Gauge Aluminum
Thickness: 0.0508 inches (1.29 mm)
Applications:
- Used for decorative panels, roofing, and fencing.
- Good for making lightweight but durable products like cans or trays.
Why Its Used: Its perfect when you need moderate strength without extra weight.
5. 18-Gauge Aluminum
Thickness: 0.0403 inches (1.02 mm)
Applications:
- Common in making aluminum foil, kitchen products, and automotive body parts.
- Often used for DIY projects like crafting and model building.
Why Its Used: Its thin and light, making it ideal for flexible and easy-to-handle products.
6. 20-Gauge Aluminum
Thickness: 0.0320 inches (0.81 mm)
Applications:
- Mostly used for lightweight sheets in products like roofing, ducts, or crafts.
- Often used in home improvement and decorative items.
Why Its Used: Its thin, flexible, and easy to shape, making it great for small and delicate projects.
Factors Influencing Gauge Choice
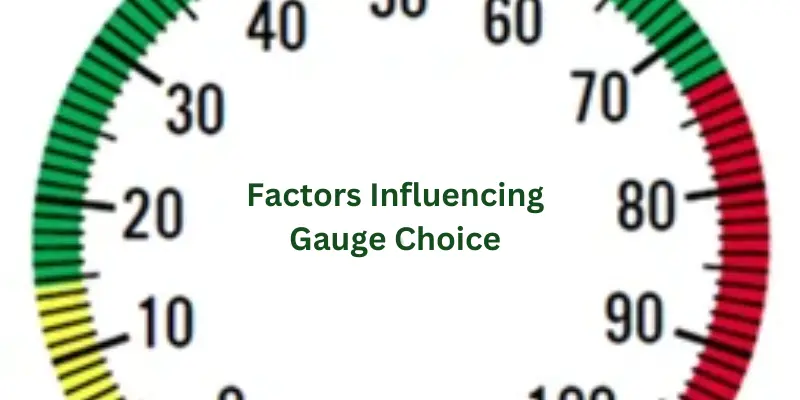
Choosing the right Sheet Metal Aluminum Gauge for your project is important. The thickness of the aluminum affects how the material will behave, how much it will cost, and how easy it will be to work with. Several factors influence your decision on which gauge to choose. Here are the main ones:
1. Strength and Durability
- Thicker gauges (like 10 or 12 gauge) are stronger and more durable. They are great for projects that need to bear heavy loads, like construction or automotive parts.
- If you need a material that can handle stress and impact without bending, you should go for a lower gauge (thicker aluminum).
- Thinner gauges (like 18 or 20 gauge) are not as strong but are still useful for lighter, less stressful tasks.
2. Weight
- Sometimes, you need aluminum that is lightweight. For example, in the aerospace industry, you need thin sheets (higher gauges) to reduce the overall weight of the aircraft.
- Thicker aluminum is heavier, which is fine for structural parts, but if you want to keep things light, thinner gauges are better.
3. Cost
- Thicker sheets are usually more expensive than thinner ones because they use more aluminum and require more resources to make.
- If your budget is tight, and the project doesn’t need thick aluminum, it’s smart to choose a thinner gauge to save money.
- Consider the cost-effectiveness when deciding on the right gauge for your project.
4. Ease of Workability
- Thinner gauges are easier to cut, bend, and shape. This makes them ideal for DIY projects, crafts, or tasks where you need to create curves and angles.
- Thicker aluminum is harder to work with, so it might require special equipment or more effort to cut and shape.
- If you need to make detailed, intricate shapes, a thinner gauge will be easier to handle.
5. Application Type
- The type of project you’re doing matters. For example:
- Structural projects, like building a bridge or industrial machinery, will need thicker aluminum for strength.
- Decorative or lightweight projects, like kitchenware or craft items, will do well with thinner aluminum.
6. Environmental Factors
- If your aluminum will be exposed to the weather or corrosive environments, you may need a gauge thick enough to resist damage.
- Thicker aluminum may perform better in outdoor or high-stress environments, while thinner gauges may be fine for indoor use.
You May Also Visit It!
Forging Process | Metal Becomes Tools and Parts – Easy Explanation
History of Nickel | From Ancient Coins to Modern Technology
Metal Does a Magnet Not Stick To | Uses and Types
Physical Properties Are Shared by Most Metals
Aluminum Gauge Conversion Chart
The Sheet Metal Aluminum Gauge conversion chart is a helpful tool that allows you to convert between different gauge systems. As we’ve discussed earlier, there are a few ways to measure aluminum thickness, and knowing how to convert between them can help make sure you’re using the right material for your project.
Heres a simple chart that shows the most common gauges used in aluminum:
Gauge | Thickness (in inches) | Thickness (in mm) |
10 | 0.1345 | 3.42 |
12 | 0.1046 | 2.66 |
14 | 0.0747 | 1.90 |
16 | 0.0508 | 1.29 |
18 | 0.0403 | 1.02 |
20 | 0.0320 | 0.81 |
Understanding the Chart
- Gauge numbers tell you how thick or thin the aluminum is. Lower numbers (like 10 gauge) represent thicker aluminum.
- The thickness column shows the exact measurement in inches and millimeters. For example, 10 gauge is 0.1345 inches or 3.42 millimeters thick.
- Different industries may use either AWG or SWG systems for measuring, so knowing the conversion can help when you’re working across different standards.
By using the chart, you can easily figure out which gauge fits your project. If you’re working with thicker metal, you’ll use lower gauge numbers, and for lighter or more flexible projects, you’ll likely choose higher gauge numbers.
Advantages and Disadvantages of Sheet Metal Aluminum Gauge
Choosing the right aluminum gauge for your project comes with several advantages and some drawbacks.
Advantages of Sheet Metal Aluminum Gauge
Advantages |
---|
Variety of Options
Strength and Durability
Lightweight
Versatility in Applications
Cost-Effective
|
Disadvantages of Sheet Metal Aluminum Gauge
Disadvantages |
---|
Strength Limitations in Thinner Gauges
Cost of Thicker Gauges
Difficult to Work with for Thicker Gauges
Limited Flexibility for Detailed Work
Environmental Considerations
|
Choosing the right Sheet Metal Aluminum Gauge depends on the specific needs of your project. While it offers several advantages like strength, versatility, and lightweight properties, its important to consider the trade-offs such as cost and workability when deciding which gauge is best.
Common FAQs About Aluminum Gauge
Here are some frequently asked questions (FAQs) to help you understand Sheet Metal Aluminum Gauge better.
1. What is the aluminum gauge system?
The Sheet Metal Aluminum Gauge system is a way to measure the thickness of aluminum sheets. The lower the number (like 10 gauge), the thicker the aluminum. As the gauge number increases (like 20 gauge), the aluminum becomes thinner. The gauge system helps people pick the right thickness for their specific projects, whether it’s for construction, automotive parts, or crafting.
2. How do I know which aluminum gauge to use?
The right aluminum gauge depends on what you’re making. For projects that need strength (like car parts or industrial equipment), use a lower gauge (like 10 or 12 gauge). If you need lighter and more flexible aluminum for something like decorative items or crafts, a higher gauge (like 18 or 20 gauge) will work better.
3. What is the difference between gauge and thickness in aluminum?
The gauge is a number that represents how thick or thin a piece of aluminum is. Lower gauges (like 10 or 12) mean the aluminum is thicker, and higher gauges (like 18 or 20) mean the aluminum is thinner. It’s important to know the gauge number because it helps you choose the right material for your project’s needs.
4. What is the most common aluminum gauge used?
The most common aluminum gauges are 16, 18, and 20. These are often used for general purposes like roofing, auto parts, and construction materials. The gauge you choose depends on whether you need something that’s lightweight or strong.
5. How do I convert between aluminum gauges?
To convert aluminum gauge to thickness in inches or millimeters, you can use a conversion chart. For example:
- 10 gauge is about 0.1345 inches or 3.42 millimeters thick.
- 20 gauge is about 0.0320 inches or 0.81 millimeters thick.
You can find conversion charts online to help you when you need to switch between gauge numbers and thickness measurements.
6. Why is it important to choose the right aluminum gauge?
Choosing the right Sheet Metal Aluminum Gauge is crucial because it affects how the aluminum will perform in your project. Thicker gauges are stronger and can bear more weight, but they’re also heavier and harder to work with. Thinner gauges are more flexible and easier to shape, but they’re not as strong. It’s important to pick the gauge that suits your project’s strength requirements, budget, and ease of use.
7. Can I use aluminum in all weather conditions?
Yes. Aluminum is resistant to rust and corrosion, which makes it perfect for outdoor use. However, thicker gauges are generally more durable in extreme weather conditions. If you’re using aluminum for something that will face harsh conditions, like a roof or vehicle parts, a thicker gauge might be the best choice.
8. How do I cut or bend aluminum based on its gauge?
Thicker Sheet Metal Aluminum Gauge (like 10 or 12 gauge) are harder to cut and bend, so you might need special tools such as a power saw or heavy-duty metal shears. On the other hand, thinner gauges (like 18 or 20 gauge) are much easier to work with and can be cut using hand tools or scissors.
9. What are some common uses for different aluminum gauges?
Here are a few common uses for different aluminum gauges:
- 10-12 gauge: Used in heavy-duty applications like structural support, automotive, and roofing.
- 14-16 gauge: Used in light construction, appliance parts, and outdoor projects.
- 18-20 gauge: Used for crafting, decorative items, and kitchenware.
10. What should I consider before buying aluminum sheets?
Before purchasing aluminum sheets, consider:
- What the material will be used for (strength, flexibility, durability).
- The environmental conditions (will it be exposed to outdoor weather?).
- Your budget (thicker aluminum may be more expensive).
- Tools available for working with aluminum (you may need special tools for thicker gauges).
These key questions, you can make a smarter choice about which aluminum gauge works best for your needs.
Conclusion
Aluminum gauge is essential when choosing the right material for your project. Whether you’re working on a heavy-duty construction task or a lightweight crafting project, picking the correct gauge ensures your aluminum performs well and meets your needs.
Remember, lower gauges are thicker and stronger, while higher gauges are thinner and more flexible. Always consider your projects requirements, the tools you have, and your budget when selecting the right gauge. By doing so, you can ensure the best results for your work.
Bonus Points
Here are some extra insights that can help you better understand and work with Sheet Metal Aluminum Gauge:
1. Durability
- Aluminums natural resistance to corrosion and rust makes it a great choice for both indoor and outdoor applications. Even in harsh environments like coastal areas, aluminum can last for years without losing its strength or appearance.
2. Recyclability
- Aluminum is one of the most recycled metals. Choosing aluminum for your project not only helps reduce waste, but it also supports the environment, as recycled aluminum uses less energy to produce than new aluminum.
3. Cost-Efficiency
- While thicker gauges might be more expensive, aluminum is still generally more affordable than other metals like steel. For projects requiring strength but at a lower cost, aluminum often provides the perfect balance.
4. Customization
- Aluminum sheets can be easily cut, shaped, and bent, making them ideal for customized applications. Whether you’re designing a unique project or a mass-produced product, aluminum can be adapted to fit specific needs.
5. Heat Resistance
- Aluminum performs well in high-temperature environments. Thicker aluminum gauges are used in parts that experience heat, like automotive engines or industrial machinery. It can withstand high heat without warping, making it a reliable material for high-heat applications.
By considering these bonus points, you’ll be even more prepared to use aluminum gauges effectively in your projects, whether for strength, cost, or environmental reasons.
You May Also Visit It!
Magnetic Materials | What Materials Are Attracted By Magnets – Benefits
Yield Strength of Metals: Types, Uses and Clear and Simple Overview
Heat Treating Steel | Key Temperatures for Hardening, Types and Uses
1075 or 1095 Steel | Find the Best Steel for Your Knife
Aluminium Metal, Types, Uses, Properties and Rust Aluminium
Please Write Your Comments