Undercut Machining | Types, Uses, Properties and Benefits
Updated: 08 Dec 2024
112
Undercut machining is a technique used to create recessed or sunken areas on a part’s surface. It allows for precise interlocking of components, making it essential in industries like aerospace and automotive. This process is done using specialized tools, such as T-slot cutters or ball-nose end mills, on CNC machines. Undercuts improve functionality, like secure fastening, weight reduction, and fluid flow, making them crucial for high-performance parts. This machining ensures parts meet specific design requirements efficiently.
What is Undercut Machining?
Undercut machining refers to the process of creating a recessed or “sunken” area on a part or workpiece that is difficult to access with standard cutting tools. This machining technique is especially important in situations where a part needs to interlock with another, or when specific shapes or cavities need to be formed to achieve a desired function or design.
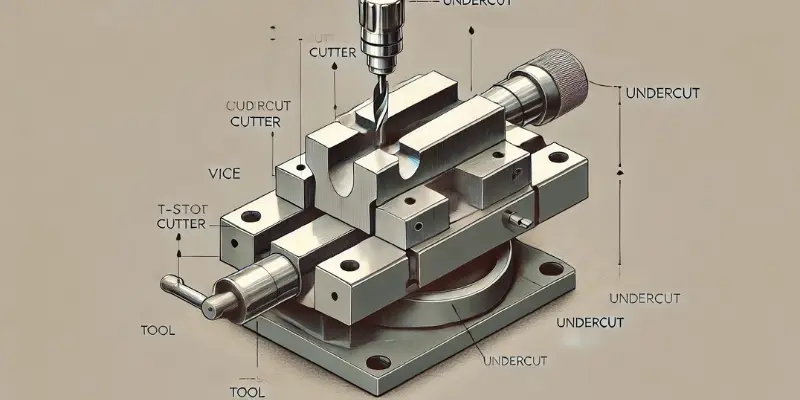
Undercut machining creates a groove or a small, detailed cavity that typically runs under a surface. These features are often required in complex parts used in industries like automotive, aerospace, or even medical device manufacturing, where components must fit together securely or need to be lightened for efficiency.
For example, think of how a bolt fits into a groove. The groove might require undercut machining to fit a particular shape or function. Special tools are used to create these features, and they can be done on CNC machines, which are highly precise and can handle complicated designs.
Undercuts are also useful in:
- Assembly efficiency: They allow parts to lock into place without the need for extra fasteners.
- Weight reduction: In industries like aerospace, where every gram counts, undercuts help reduce the material used without sacrificing strength.
- Fluid and gas pathways: Certain undercuts are designed to allow liquids or gases to flow through machinery or components.
The technique itself requires careful planning and specialized machinery to ensure accuracy and precision, as undercuts can be tricky to machine due to their unique and often intricate shapes.
You May Also Visit It
Copper Zinc Alloys – Step by Step Guide
Cast Iron Melting Temp | Discover Its Industrial Secrets
Is Aluminium Magnetic Material | Types, Uses and Properties
Physical Properties Are Shared by Most Metals
Why Is Undercut Important in Machined Parts?
- Undercuts are a crucial feature in machining, used to create intricate shapes and improve the functionality of parts. You might not notice them at first glance, but they play a significant role in many industries, from automotive to aerospace. Here’s why they matter:
- Enhanced Assembly and Fit One of the main reasons for using an undercut is to make sure parts fit together securely. An undercut allows two components to lock in place, often without the need for extra fasteners like screws or bolts. This not only saves time but also reduces the number of parts required, which is especially beneficial in complex assemblies.
- Weight Reduction In industries like aerospace, where every gram counts, undercuts are incredibly useful. By removing unnecessary material while maintaining strength, they help reduce the weight of parts. This can lead to improved fuel efficiency, increased payload capacity, and overall better performance.
- Better Functionality in Hydraulic Systems Undercuts are essential in hydraulic systems, where they create pathways for the flow of liquids or gases. These pathways allow for smooth and controlled movement, which is vital for the performance of pumps, valves, and other components that rely on precise fluid movement.
- Design Flexibility Undercuts give designers the flexibility to create parts with more complex geometries. For example, they enable the creation of internal cavities and intricate features that would be impossible to achieve with basic machining. This flexibility can be especially important in fields like medical device manufacturing, where precise, customized parts are often required.
- Improved Part Strength By strategically removing material in specific areas, undercuts can help reduce stress concentrations, especially around components like bearings or shafts. This helps prevent failures and ensures parts perform reliably under load, which is crucial for high-performance machinery.
- Cost-Effective Manufacturing While machining undercuts can be more complex and require specialized tools, they can ultimately reduce costs by eliminating the need for additional parts, fasteners, or assembly processes. They also allow for more efficient use of materials, which can lead to cost savings over time.
Undercuts are more than just a design feature they are an essential part of modern machining that enhances functionality, improves part performance, and helps reduce production costs. Whether you’re looking to improve part assembly, reduce weight, or create more intricate designs, understanding the importance of undercuts can make a big difference in the overall success of your project.
History of Undercut Machining
Undercut machining has a long history that reflects the evolution of manufacturing processes. The term “undercut” refers to a recessed or sunken feature that is cut into a material, typically metal, in the machining process. While undercuts have existed for centuries in various forms, their role in modern manufacturing became more prominent with the development of advanced machining technologies.
Manual methods such as filing and turning were the primary ways to create intricate features like undercuts. These techniques, while effective for simple designs, were limited in their precision and efficiency. It wasn’t until the introduction of machines like the lathe and milling machine during the Industrial Revolution that more complex shapes, including undercuts, could be produced at scale.
By the mid-20th century, CNC (Computer Numerical Control) machines revolutionized the way undercuts were created. CNC machines, which are controlled by computers, allowed manufacturers to achieve much higher precision and flexibility. These machines could easily handle complex geometries, including the precise angles and shapes required for undercuts, without the need for extensive manual intervention. This shift made undercut machining more accessible to a wider range of industries.
Undercut machining has since become essential in various fields such as aerospace, automotive, and medical manufacturing, where the need for precise, interlocking components has grown. With the advent of multi-axis machining, which allows tools to move in multiple directions, the creation of undercuts has become even more sophisticated. These advancements have enabled the production of lightweight parts, improved assembly processes, and enhanced the functionality of complex mechanical systems.
Undercut machining is a standard practice in many high-precision manufacturing environments, where its role in improving part performance and reducing material waste is critical. As technology continues to evolve, the ability to design and create undercuts with increasing accuracy remains a cornerstone of modern machining techniques.
Types of Undercuts Machining
When it comes to machining, undercuts are unique shapes or grooves created in a workpiece. These features are essential for many industries, but understanding the different types of undercuts can be tricky. Here’s a simple breakdown of the most common types of undercut machining:
1. T-Slot Undercut
- What it is: A T-slot undercut is shaped like the letter “T.” It’s typically used in situations where parts need to be joined together using bolts. The T-slot allows a bolt to slide into the groove, making the connection secure.
- Why it’s useful: This undercut is particularly common in machinery and equipment assembly because it allows easy attachment and adjustment of parts.
2. One-Sided Undercut
- What it is: This type of undercut only affects one side of the workpiece. It’s often used for creating grooves or channels that are meant to fit specific components, such as seals or rings.
- Why it’s useful: It’s particularly helpful when you need to precisely fit parts together, especially for tight seals in mechanical applications.
3. Dovetail Undercut
- What it is: A dovetail undercut has a wedge-like shape, often used for joining two components. The tapered edges lock the parts securely, making them highly resistant to shifting or loosening.
- Why it’s useful: This undercut is very popular in woodworking, but also used in metalworking for strong, reliable connections between parts.
4. Tapered Undercut
- What it is: A tapered undercut features a sloping surface that gradually changes from one side to the other. It’s commonly used when parts need to fit snugly with a gradual frictional force.
- Why it’s useful: The smooth tapering allows parts to slide or press into place, making it ideal for mechanical parts where smooth motion is key.
5. Spherical Undercut
- What it is: A spherical undercut has a rounded, ball-like shape. This is often used in components that require rotation, like ball joints or bearings.
- Why it’s useful: The spherical shape helps with smooth movement, allowing parts to rotate or swivel with minimal friction.
6. Keyway Undercut
- What it is: This undercut creates a slot in which a key is inserted to lock two rotating components together. It’s commonly used in shafts and gears.
- Why it’s useful: Keyways are critical for transmitting torque between parts, ensuring they rotate together without slipping.
7. Relief Undercut
- What it is: A relief undercut is used to reduce stress in parts, often around bearings or shafts. It’s a small groove or recess designed to provide clearance and reduce wear.
- Why it’s useful: This type of undercut is important in preventing damage and ensuring smooth movement in rotating parts.
Each type of undercut serves a specific purpose depending on the needs of the design. Whether you are working with components that need to fit securely, slide into place, or rotate smoothly.
Making Process of Undercut Machining
Undercut machining is a process that involves creating a recessed area or groove in a workpiece, often essential for the function or design of mechanical parts. This technique is widely used across industries, especially when interlocking or complex component designs are needed. Here’s a breakdown of how it works:
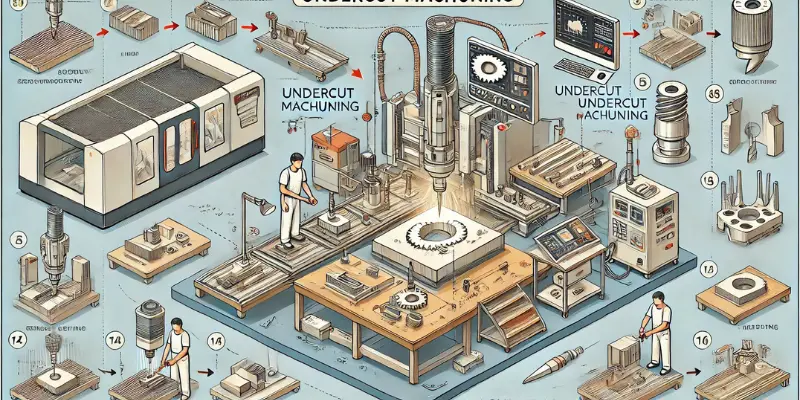
- Preparation of Materials Before starting, the material (often metal or plastic) is carefully chosen based on the part’s requirements. The next step is to ensure that the material is properly set up and securely clamped in the machine to avoid movement during the cutting process.
- Setting Up the Machine The CNC (Computer Numerical Control) machine is set up to make the specific undercut. Using specialized software, the design of the part is entered into the system, which controls the machining path. The machine may require the attachment of certain tools, like an end mill or a specific cutter, depending on the type of undercut being created.
- Selecting the Right Tool Tools such as T-slot cutters, lollipop cutters, or ball-nose end mills are selected based on the shape of the undercut needed. For example, T-slot cutters are used for creating slots, while lollipop cutters are great for one-sided undercuts. The tool must be designed to reach the specific recessed area of the workpiece.
- Machining the Undercut Once everything is set up, the CNC machine begins the machining process. The cutting tool follows the programmed path to carefully carve out the undercut. The cutting action might happen in multiple passes to ensure accuracy, particularly for complex shapes or tight tolerances.
- Inspection and Quality Control After machining, the part is carefully inspected to ensure it meets all the required dimensions and tolerances. Since undercuts are often critical to the function of the part, the inspection process helps verify that the machining has been done correctly, ensuring that the part fits perfectly in its assembly or performs as needed.
- Post-Processing In some cases, the part may need additional processing, such as deburring, polishing, or coating. This step ensures that the surface of the undercut is smooth, free from sharp edges, and ready for final assembly or further use.
The process of undercut machining allows for creating precise, complex shapes that are essential for various industries. It requires careful setup, tool selection, and inspection to ensure the quality of the final part. By understanding this process, manufacturers can produce components that meet high standards of precision and functionality.
You May Also Visit It
What is Ferrous vs Non Ferrous Metals – Complete Guide
What is Titanium Steel – Types, Uses, Properties and Modern Metal
Plasma Cutter How Does It Work – Complete Guide
Is Copper a Metalloid | Understanding the Classification of Elements
Applications of Undercut Machining
Undercut machining plays a crucial role in a wide range of industries, helping to create parts with specific features that are necessary for efficient and effective operation. Here’s how undercut machining is applied across different sectors:
- Aerospace Industry In aerospace manufacturing, precision is critical. Undercuts are used to reduce the weight of parts while maintaining strength and functionality. For example, they are applied in components like brackets, turbine blades, and housings, where material can be removed without compromising structural integrity. This technique helps reduce overall weight, improving fuel efficiency and performance of aircraft.
- Automotive Sector The automotive industry relies on undercuts for components that require secure assembly, such as parts that need to lock into one another without external fasteners. Additionally, undercuts help to create internal pathways in parts like engine components, where fluids or gases need to flow efficiently, such as in cooling systems.
- Medical Devices In the production of medical implants, precision undercut machining is essential. It allows for the creation of parts like joint replacements or surgical tools, which must fit precisely and have specific geometric features for functionality. Undercuts are used to ensure that parts interlock or fit snugly within the body or other components without gaps.
- Hydraulic Systems Undercuts are critical in hydraulic systems for creating fluid channels within a part. These channels ensure the smooth flow of liquids or gases that are essential for the system’s operation. Components like pistons, valves, and cylinders often feature undercuts to manage these fluid pathways effectively.
- Tooling and Fixtures Specialized tooling and fixtures, such as jigs or clamps, are often designed with undercuts to securely hold parts during the manufacturing process. These undercuts allow for the easy insertion of fasteners or bolts while keeping the components firmly in place during machining.
- Electronics and Consumer Goods In electronics, undercuts are used to create precise fittings in casings, brackets, or internal connectors. This ensures that all parts fit together smoothly, improving the device’s overall assembly and durability. Similarly, in consumer goods manufacturing, undercuts can enhance the functionality and aesthetics of items by allowing for precise fitting or providing a clean and seamless design.
- Mechanical Assemblies Undercuts are also widely used in mechanical assemblies, particularly where parts need to fit together tightly for strength or to prevent movement. For example, in automotive gear systems or industrial machinery, undercuts help to ensure that the components interlock without the need for additional fasteners or adhesives, reducing assembly time and cost.
- Molds and Dies In mold and die manufacturing, undercuts are often used to create complex shapes that are essential for the final product. Undercuts allow for the removal of molded parts without damaging their structure. This application is critical in the production of plastic parts, such as bottle caps, containers, and toys.
Undercut machining is an essential technique used in many industries to create precise, functional, and efficient parts. Whether it’s in aerospace, automotive, medical, or other fields, undercuts are vital for producing components that need to fit together or perform specific functions while reducing material usage or enhancing strength.
Challenges in Undercut Machining
- Undercut machining, while offering many benefits, also presents certain challenges that need careful consideration. One of the most significant hurdles is tool wear. Undercuts often require specialized tools like ball-nose or T-slot cutters, and these tools can wear down more quickly when used on hard materials or for intricate designs. This can lead to higher maintenance costs and the need for frequent tool replacement.
- Another challenge is material limitations. Some materials, especially those that are brittle or too tough, may pose difficulties during machining. These materials can cause the tool to deflect, leading to inaccurate cuts or even tool damage. Choosing the right material for both the workpiece and the cutting tools is critical for minimizing such issues.
- Precision is also a concern. Undercut machining often requires tight tolerances to ensure that parts fit together perfectly, especially when they’re part of an assembly. Achieving the desired precision can be challenging, particularly in high-volume production, where small variations can add up over time. This is why modern machines, such as CNC machines with multi-axis capabilities, are increasingly used to maintain the necessary accuracy.
- Additionally, setup time can be another challenge. Depending on the complexity of the undercut, the setup process can take longer, particularly when switching between different cutting tools or adjusting settings on a CNC machine. This can slow down production, especially for small batches or custom jobs.
- Lastly, cost efficiency is a concern for many manufacturers. While undercut machining offers functional and design advantages, the process can be more expensive due to the need for specialized tools, high precision, and longer setup times. Balancing quality with cost is essential to ensure the process remains economically viable.
Benefits of Undercuts
Undercuts offer several advantages in machining that make them essential in many industries. Here’s a breakdown of their key benefits:
Benefits |
---|
|
Drawback of Undercut Machining
Undercut machining can be a valuable tool, but it comes with its challenges. The complexity and precision required may lead to increased production costs and time.
Drawback |
---|
|
Quality Control in Undercut Machining
When machining undercuts, it’s crucial to ensure the final product meets exact specifications. Here’s a breakdown of key quality control steps to follow:
- Measurement Accuracy: Ensure the undercut dimensions match the design specifications. Use precise measuring tools like micrometers or laser gauges.
- Surface Finish Check: The surface of the undercut should be smooth, with no visible defects. This is essential for the part’s functionality and appearance.
- Tolerance Verification: Confirm that the undercut is within the required tolerance limits, especially in parts where tight fits are critical.
- Inspection Methods: Utilize automated or manual inspection methods, such as 3D scanning, to check the quality of hard-to-reach undercuts.
- Tool Condition: Regularly inspect and replace worn tools, as dull cutters can affect the accuracy and quality of the undercut.
- Dimensional Stability: Ensure the undercut maintains dimensional stability throughout the machining process, especially with material that may warp or shrink.
- Test Fitting: For parts that need to fit together, test the undercut with the mating component to ensure it fits correctly.
Future Trends in Undercut Machining
Undercut machining continues to evolve with new technologies. Here’s a look at some exciting future trends:
1. Automation & AI Integration
- More machines are using AI for faster, more precise undercutting, reducing human error.
- AI tools can adapt to various material types, optimizing tool paths in real-time.
2. Additive Manufacturing
- 3D printing is being explored to create parts with undercuts that traditional machining couldn’t achieve.
- This allows for more complex designs and faster production cycles.
3. Multi-Axis CNC Machines
- Future CNC machines will continue to advance in their ability to handle undercuts from multiple angles, improving precision and efficiency.
4. Improved Materials
- The development of stronger, lighter materials means undercuts will play an even more vital role in industries like aerospace and automotive, where weight and durability are crucial.
5. Energy Efficiency
- New methods are making undercut machining more energy-efficient, helping industries meet sustainability goals without compromising quality.
Common FAQs about Undercut Machining
What is Undercut Machining?
- Undercut machining is a process where special tools are used to carve or cut materials (like metal or plastic) in a way that creates spaces or shapes under a surface. Think of it like cutting a small tunnel or groove in a block of material.
Why is Undercut Machining Important?
- It’s important because it helps make parts more precise, allows for unique shapes, and can improve the way things fit together, especially in machines and cars.
How Does Undercut Machining Work?
- In undercut machining, a machine called a “milling machine” uses sharp tools to cut into materials. These tools move in different directions to create the undercuts.
What Materials Can Be Machined with Undercuts?
- Most metals like aluminum and steel, as well as plastics, can be machined with undercuts. These materials are shaped into the right forms using the process.
When Do We Use Undercut Machining?
- We use undercut machining when we need to make complex shapes, like parts of a toy, engine components, or even jewelry, that can’t be made with just simple cuts.
Is Undercut Machining Hard to Do?
- Yes, it can be tricky because the tools need to move in the right direction to avoid damaging the material. It requires skill and special machines.
Can Undercut Machining Be Done on Small Parts?
- Yes, undercuts can be made on both small and large parts. It depends on the machine and tools used.
What Are the Benefits of Undercut Machining?
- It makes parts fit better, works well for creating special shapes, and can even help in saving space in complex designs.
What Are Some Challenges with Undercut Machining?
- Sometimes, it can be hard to get the exact shape you want. Also, it might take longer to do than regular cutting or drilling.
Who Uses Undercut Machining?
Engineers, manufacturers, and people who build things like cars, airplanes, or computers use undercut machining to make parts that need to fit or work perfectly.
Conclusion
Undercut machining is like using a special tool to carve tricky shapes and spaces in materials like metal and plastic. It helps make cool and useful things like car parts, toys, and even tiny pieces for computers. While it can be a bit challenging, it’s super important for making things fit together perfectly and work well.
Just like drawing takes practice to make it perfect, undercut machining needs skilled workers and smart machines. It shows how creativity and technology come together to build amazing things around us.
You May Also Visit It
Cast Iron Melting Temp | Discover Its Industrial Secrets
Metal Stamping Aluminum | Easy Steps to Understand Metal Stamping
Diagram of V8 Engine Explore the Power Behind Every Part
Welding Position | Types, Properties and Uses – Pros and Cons
What is Cold Roll Steel: Types, Grades and Uses | Pros and Cons
Please Write Your Comments